Brief Process
Composite pipes are manufactured through a process that involves several stages, including fiber production, resin preparation, fiber preparation, winding, resin impregnation, curing, post-curing treatment, testing, and finishing. Here’s a more detailed overview of the manufacturing process:
Stage 1: Fiber Production
- Fibers such as glass, carbon, or aramid are produced through various methods, including pultrusion, extrusion, or textile production.
- The fibers are cut to length, cleaned, and treated with chemicals or coatings to enhance bonding with the resin.
Stage 2: Resin Preparation
- The resin is mixed with additives, such as hardeners, accelerators, and fillers, to create a workable compound.
- The resin mixture is degassed to remove air bubbles and improve its flowability.
Stage 3: Fiber Preparation
- The fibers are wound onto a mandrel or mold, which is shaped like the desired pipe.
- The fibers are wound in a specific pattern, such as helical or circumferential, to achieve the desired properties.
Stage 4: Winding
- The fibers are wound onto the mandrel or mold, layer by layer, to achieve the desired thickness and properties.
- The winding process can be done manually or using automated machinery.
Stage 5: Resin Impregnation
- The resin is applied to the fibers, either by hand layup, infusion, or pultrusion.
- The resin saturates the fibers, binding them together to form a strong and durable composite material.
Stage 6: Curing
- The pipe is placed in a mold or autoclave, where heat and pressure are applied to cure the resin.
- The curing process can take several hours or days, depending on the resin and desired properties.
Stage 7: Post-Curing Treatment
- The pipe is removed from the mold and excess resin is trimmed.
- The pipe may undergo additional treatments, such as sanding, painting, or applying a liner.
Stage 8: Testing and Inspection
- The pipe is tested for strength, durability, and performance under various conditions.
- Samples are checked for chemical composition, dimensions, and other specifications.
Stage 9: Finishing
- The pipe is packaged and prepared for shipping.
- Fittings, such as couplings and adapters, are attached as needed.
Market Introduction
The global composite pipes market has experienced significant growth in recent years, driven by increasing demand from various industries, including oil and gas, water treatment, chemical processing, aerospace, automotive, and construction. The market is expected to continue its growth trajectory, driven by the need for corrosion-resistant, lightweight, and durable piping solutions.
Market Size and Growth
The global composite pipes market size was valued at USD 3.4 billion in 2020 and is expected to grow at a Compound Annual Growth Rate (CAGR) of 7.5% from 2021 to 2028.
Drivers and Trends
- Increased Demand from Oil and Gas Industry: The oil and gas industry is a significant consumer of composite pipes, driven by the need for corrosion-resistant and high-pressure piping solutions.
- Growing Adoption in Water and Wastewater Treatment: Composite pipes are increasingly being used in water and wastewater treatment applications due to their resistance to corrosion and ability to withstand harsh environments.
- Rising Demand from Aerospace and Automotive Industries: Composite pipes are used in aerospace and automotive applications due to their lightweight and high-strength properties.
- Increasing Focus on Sustainability and Energy Efficiency: Composite pipes are being used in renewable energy applications, such as wind turbines and hydroelectric power plants, due to their ability to withstand harsh environments and reduce maintenance costs.
- Advancements in Materials and Manufacturing Technologies: Advances in materials science and manufacturing technologies have improved the performance and affordability of composite pipes, driving their adoption across industries.
Recommended Glass Fibre
JUSHI Direct Rovings for Filament Winding
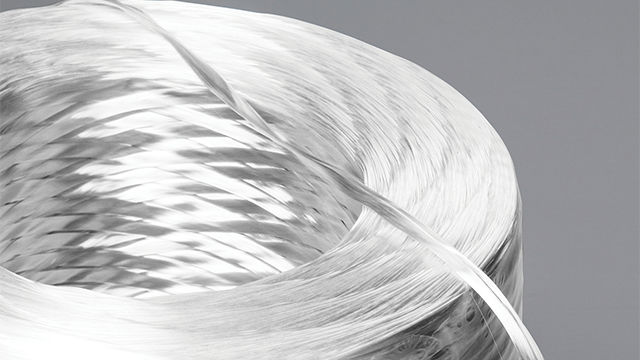